Welcome to My Blog!
Before we dive into the content, I’d love for you to join me on my social media platforms where I share more insights, engage with the community, and post updates. Here’s how you can connect with me:
Facebook:https://www.facebook.com/profile.php?id=61565500692293
Now, let’s get started on our journey together. I hope you find the content here insightful, engaging, and valuable.
Table of Contents
Introduction
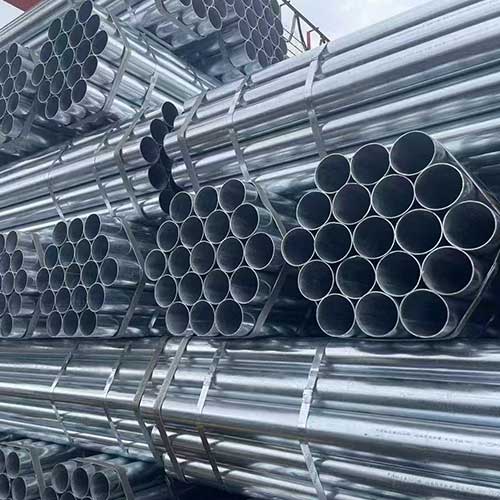
The galvanizing process is a widely used industrial method for protecting metal, particularly steel, from corrosion and rust. By applying a zinc coating to metal surfaces, galvanization extends the lifespan of steel products, making them more durable and resistant to environmental factors. From infrastructure and construction to automotive and manufacturing, the galvanizing process plays a critical role in industries that rely on strong and long-lasting materials. This guide provides a comprehensive overview of the galvanizing process, its types, key benefits, applications, and everything you need to know about how it works. Whether you are new to the concept or looking to deepen your understanding, this article is your one-stop resource.
What Is the Galvanizing Process?
The galvanizing process involves coating a metal surface with a protective layer of zinc. This zinc coating acts as a barrier, preventing oxygen and moisture from reaching the underlying metal and thereby reducing the risk of corrosion. The process has been widely used since the 19th century and continues to be essential in modern industries due to its reliability and cost-effectiveness. There are several types of galvanizing processes, each with unique characteristics and applications. The most common methods include hot-dip galvanizing, electro-galvanizing, and thermal spray galvanizing.
Types of Galvanizing Processes
Hot-Dip Galvanizing
Hot-dip galvanizing is the most common and widely used method. In this process, steel is immersed in molten zinc at high temperatures, usually around 450°C (842°F). As the steel is removed from the bath, the zinc reacts with the surface of the metal, forming a strong metallurgical bond. The result is a durable, corrosion-resistant coating that is ideal for outdoor and industrial applications.
Advantages:
- Provides a thick, uniform coating
- Offers long-term protection
- Suitable for large steel structures
Electro-Galvanizing
Electro-galvanizing, also known as electroplating, involves applying a thin zinc coating to steel using an electrical current. This process is carried out at room temperature, making it energy-efficient. Unlike hot-dip galvanizing, electro-galvanizing produces a thinner but more precise coating, making it suitable for smaller components.
Advantages:
- Ideal for precision applications
- Produces a smooth surface finish
- Allows for consistent thickness control
Thermal Spray Galvanizing
Thermal spray galvanizing involves spraying molten zinc onto the surface of the steel using a specialized spray gun. This method is commonly used for repairing galvanized coatings or coating complex shapes that are difficult to dip in molten zinc.
Advantages:
- Suitable for localized repairs
- Can be applied to irregularly shaped components
- Offers flexibility in coating thickness
How the Galvanizing Process Works: Step-by-Step
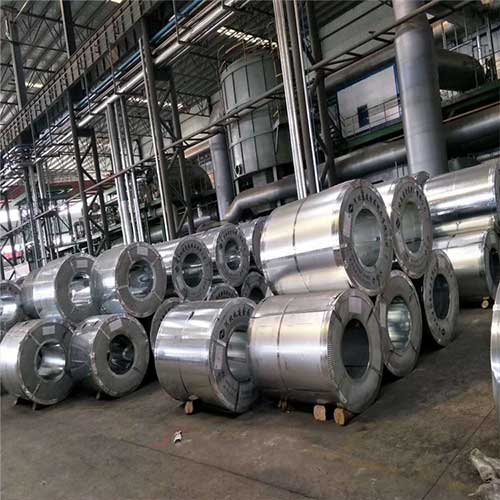
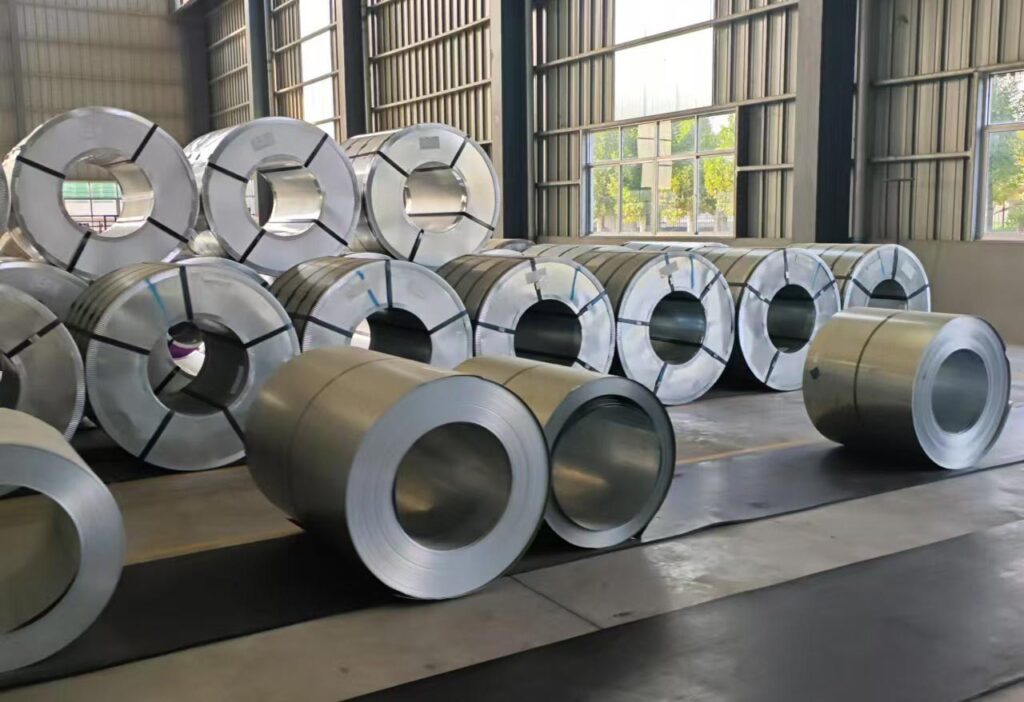
Each type of galvanizing process follows specific steps to ensure the metal surface is adequately prepared and coated. The general steps for the hot-dip galvanizing process are outlined below:
- Surface Preparation
The surface is cleaned to remove dirt, grease, and rust. This typically involves a combination of degreasing, pickling (acid cleaning), and fluxing to ensure the steel is chemically clean before galvanizing. - Immersion in Molten Zinc
The prepared steel is dipped into a bath of molten zinc at high temperatures. The zinc reacts with the steel to form intermetallic layers that are tightly bonded to the surface. - Cooling and Inspection
After the coating is applied, the steel is cooled in water or air to solidify the zinc layer. The coated product is then inspected for quality assurance, ensuring that the coating is uniform and free from defects.
Key Benefits of the Galvanizing Process
The galvanizing process offers several advantages, making it a preferred choice for protecting metal surfaces. Below are the key benefits:
Corrosion Resistance
The zinc coating provides excellent protection against rust and corrosion, extending the lifespan of steel products in harsh environments.
Low Maintenance
Galvanized steel requires minimal maintenance, reducing long-term costs for industrial and commercial applications.
Durability
The metallurgical bond between zinc and steel ensures that the coating remains intact even in extreme conditions.
Cost-Effectiveness
Compared to other corrosion-protection methods, the galvanizing process is affordable and offers a high return on investment due to its long-lasting performance.
Environmentally Friendly
Galvanized steel is recyclable and has a lower environmental impact compared to other coating methods.
Applications of Galvanized Steel
Galvanized steel is used in a wide range of applications across various industries. Below are some of the most common uses:
- Construction: Structural beams, roofing, and cladding
- Automotive: Body panels, frames, and fasteners
- Agriculture: Fencing, storage tanks, and equipment
- Energy: Transmission towers and pipelines
- Transportation: Bridges, guardrails, and railway tracks
Table: Comparison of Galvanizing Methods
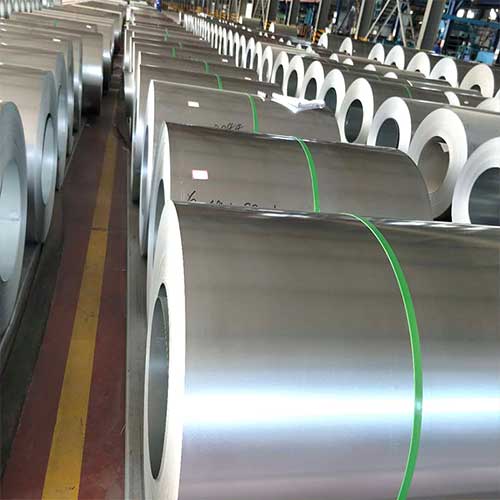
Aspect | Hot-Dip Galvanizing | Electro-Galvanizing | Thermal Spray Galvanizing |
---|---|---|---|
Coating Thickness | Thick | Thin | Variable |
Durability | High | Moderate | High |
Surface Finish | Matte | Smooth | Rough |
Applications | Large structures | Precision components | Repairs, irregular shapes |
Cost | Moderate | Low | High |
Conclusion
The galvanizing process is a proven method for enhancing the durability and longevity of steel products. By providing robust protection against corrosion, galvanized steel is an essential material in industries ranging from construction and automotive to energy and agriculture. Understanding the different types of galvanizing processes and their benefits can help you choose the right method for your specific application. Whether you require hot-dip galvanizing for structural beams or electro-galvanizing for small components, this versatile process ensures long-term reliability.
FAQ
What is the purpose of galvanizing?
The purpose of galvanizing is to protect metal surfaces, particularly steel, from corrosion and rust. The zinc coating acts as a barrier, preventing moisture and oxygen from reaching the steel.
How long does galvanized steel last?
The lifespan of galvanized steel depends on environmental factors and the thickness of the zinc coating. In general, it can last 20 to 50 years or more in most environments.
Can galvanized steel be painted?
Yes, galvanized steel can be painted, but it requires proper surface preparation to ensure the paint adheres effectively.
What are the limitations of the galvanizing process?
The galvanizing process is not suitable for high-temperature environments or applications where a highly decorative finish is required. Additionally, it may not be cost-effective for small production runs.
Is galvanized steel environmentally friendly?
Yes, galvanized steel is environmentally friendly. It is recyclable and reduces the need for frequent replacement, lowering the environmental impact over time.
What metals can be galvanized?
While steel is the most common metal used in the galvanizing process, other metals, such as iron, can also be galvanized.