Welcome to My Blog!
Before we dive into the content, I’d love for you to join me on my social media platforms where I share more insights, engage with the community, and post updates. Here’s how you can connect with me:
Facebook:https://www.facebook.com/profile.php?id=61565500692293
Now, let’s get started on our journey together. I hope you find the content here insightful, engaging, and valuable.
Table of Contents
Introduction
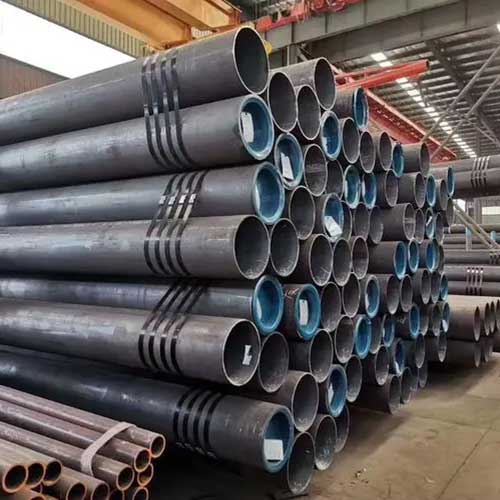
When it comes to the installation of underground gas lines, choosing the right material for the pipe is essential. The underground gas line pipe must be durable, resistant to environmental conditions, and meet safety standards to ensure a reliable and safe gas distribution system. The wrong choice of materials can result in safety hazards, increased maintenance costs, or even catastrophic failure.
This blog will explore the factors to consider when selecting the best material for an underground gas line pipe. It will cover the various materials used for underground gas lines, their pros and cons, and what to keep in mind when choosing the right option for your project.
What is an Underground Gas Line Pipe?
An underground gas line pipe is a pipe that is installed underground to carry natural gas or other gases from a distribution system to homes, businesses, and industrial facilities. These pipes are typically buried several feet below the surface to avoid external damage and to minimize the risk of gas leaks. The material used for these pipes must withstand underground conditions, including soil pressure, moisture, and potential chemical exposure, without compromising the safety or efficiency of the gas transport system.
Common materials used for underground gas line pipes include:
- Steel
- Copper
- Polyethylene (PE)
- Polyvinyl Chloride (PVC)
- Ductile Iron
The selection of the right material depends on a variety of factors, including the type of gas being transported, the soil conditions, environmental considerations, and budget.
Factors to Consider When Choosing an Underground Gas Line Pipe
Durability and Longevity
One of the most important factors to consider when choosing an underground gas line pipe is its durability and longevity. Underground pipes are subject to various environmental stresses, such as pressure from the soil, temperature fluctuations, and potential exposure to chemicals and moisture. The chosen material must be capable of withstanding these factors for an extended period of time.
Key factors that affect the durability of underground gas line pipes include:
- Corrosion resistance: The material must be resistant to corrosion, especially in areas where soil moisture or chemicals may cause degradation.
- Pressure resistance: The pipe must withstand the pressure exerted by the surrounding soil and the gas flowing through it.
- Environmental conditions: Extreme temperatures, shifting soils, or exposure to harsh chemicals may compromise the pipe’s integrity.
Safety Considerations
Safety is the primary concern when installing an underground gas line pipe. The material must not only ensure a secure connection but also prevent leaks or failures that could lead to dangerous situations, such as gas leaks, explosions, or fires.
Considerations for safety include:
- Leak resistance: The material should prevent gas from leaking under pressure. Leaks are a major safety hazard, so the pipe should be tightly sealed.
- Fire resistance: The material should not be easily combustible, as gas is highly flammable. In the event of a leak, the pipe should not contribute to the spread of fire.
- Flexibility and impact resistance: The pipe should have the flexibility to withstand ground shifts or impacts from external forces without cracking or breaking.
Cost and Budget
While safety and durability are critical, the cost of the underground gas line pipe is also an important consideration. Different materials come with varying costs, and the selection will depend on your budget, the size of the project, and the long-term investment.
Factors that influence the cost include:
- Material cost: Some materials, such as steel and ductile iron, tend to be more expensive than others like polyethylene (PE) and PVC.
- Installation costs: The ease of installation and the need for special equipment may affect the overall cost of the project.
- Maintenance costs: Some materials may require more frequent inspections and repairs, increasing the long-term costs.
Resistance to Corrosion
Corrosion is a significant issue for underground gas line pipes, especially when exposed to moisture, soil acidity, or chemicals. Corroded pipes can lead to leaks and system failures. Therefore, choosing a material that resists corrosion is vital to ensure the pipe’s long-term integrity.
Materials with high corrosion resistance include:
- Polyethylene (PE): PE is highly resistant to corrosion and is commonly used for underground gas lines.
- Copper: Copper is also known for its resistance to corrosion and is often used in smaller gas line systems.
- Steel and ductile iron: These materials may require special coatings or linings to protect against corrosion.
Table: Comparison of Materials for Underground Gas Line Pipes
Material | Durability | Corrosion Resistance | Safety | Cost | Common Applications |
---|---|---|---|---|---|
Steel | High | Moderate (requires coatings) | High (but requires protective measures) | Moderate to High | Industrial gas distribution, high-pressure systems |
Copper | Moderate | High | High | High | Residential gas lines, small installations |
Polyethylene (PE) | High | Very High | High | Low | Residential and commercial installations, low-pressure systems |
Polyvinyl Chloride (PVC) | Moderate | Moderate (requires protection) | Moderate | Low | Low-pressure systems, not ideal for high-pressure gas lines |
Ductile Iron | Very High | Moderate (requires protection) | High | High | Industrial and municipal systems, heavy-duty applications |
Best Practices for Installing Underground Gas Line Pipes
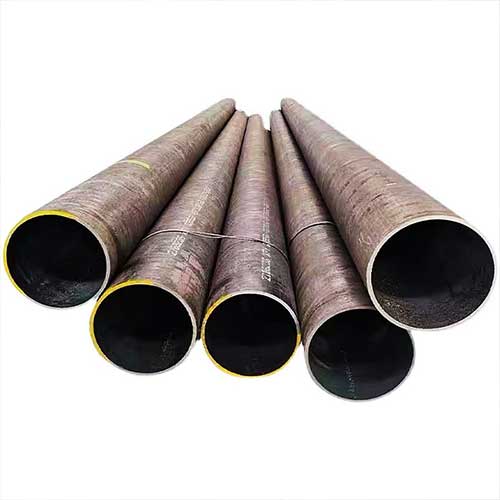
Proper Trenching
One of the most crucial aspects of installing underground gas line pipes is trenching. The trench should be dug to the appropriate depth and width to allow for easy installation and to prevent damage to the pipe. It is also essential to ensure that the pipe is buried deep enough to avoid being affected by surface traffic, weather conditions, or other external factors.
Proper Material Handling
Handling the material carefully during installation is critical to avoid damage that could compromise the pipe’s integrity. Materials like steel or ductile iron are susceptible to bending or cracking if mishandled, while polyethylene is flexible but can be damaged by sharp objects.
Regular Inspection and Maintenance
Once the gas line is installed, regular inspections and maintenance are essential to detect any potential issues such as corrosion, wear, or leaks. Ensuring that the pipe is in good condition helps avoid costly repairs and maintains the safety of the gas system.
Conclusion
Choosing the right material for an underground gas line pipe is a crucial decision that directly impacts the safety, durability, and cost of the project. Materials such as polyethylene, steel, and ductile iron are commonly used in underground gas line installations, each offering unique advantages depending on the specific requirements of the project.
Considerations like corrosion resistance, safety, cost, and the expected lifespan of the pipe should guide your decision. It’s essential to work with a professional to select the material best suited for your project, ensuring that your underground gas line is reliable and secure for years to come.
FAQ
What is the best material for underground gas line pipes?
The best material for underground gas line pipes depends on the specific needs of the project. Polyethylene (PE) is a popular choice due to its corrosion resistance and cost-effectiveness. Steel and ductile iron are also used for high-pressure applications.
Why is corrosion resistance important for underground gas lines?
Corrosion resistance is vital because corroded pipes can lead to gas leaks, which are a significant safety hazard. Choosing a material with good corrosion resistance helps ensure the pipe remains intact for years.
How deep should underground gas pipes be buried?
The depth at which underground gas pipes should be buried depends on local regulations, but they are typically buried at least 18-24 inches deep to avoid damage from external forces and to maintain safety.
Can I use PVC for underground gas lines?
PVC is generally not recommended for underground gas lines, especially for high-pressure systems, as it lacks the durability and safety required for gas transport. However, it may be suitable for low-pressure applications in some areas.
How often should underground gas lines be inspected?
Underground gas lines should be inspected regularly as part of a routine maintenance schedule. The frequency of inspections depends on the material, environmental factors, and the age of the system.
Can polyethylene be used for high-pressure gas lines?
Polyethylene is typically used for low- to medium-pressure systems. For high-pressure gas lines, materials like steel or ductile iron are preferred due to their strength and ability to handle higher pressures.
How do I know if my underground gas line needs repair?
Signs of a damaged underground gas line may include gas odors, pressure drops, or visible damage to the pipe. If you suspect a problem, it’s essential to contact a professional for inspection and repair.