مقدمة
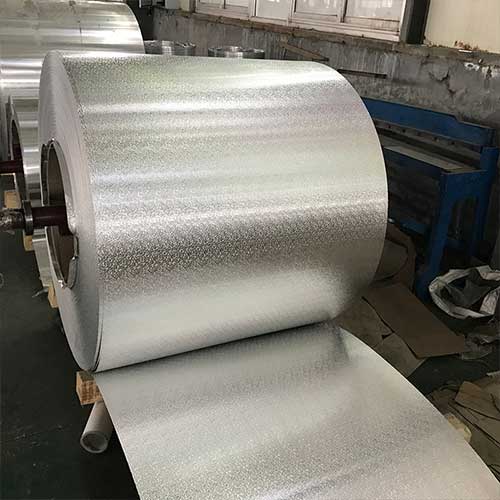
Aluminum coils are an essential component in industries ranging from construction to automotive and packaging. Their lightweight properties, corrosion resistance, and versatility make them highly sought after in modern manufacturing. But how exactly are aluminum coils manufactured? This comprehensive guide explores the step-by-step process of aluminum coil production, from raw material extraction to the finished product. Whether you’re in the manufacturing industry or simply curious about aluminum coils, this article will provide you with all the details you need.
ما هي Aluminum Coils?
Aluminum coils are continuous strips of aluminum that are rolled, treated, and coiled for transportation and further processing. They serve as raw materials for a wide range of products, such as aluminum sheets, plates, and foils.
The Manufacturing Process of Aluminum Coils
Mining and Refining Aluminum
Aluminum production begins with bauxite mining, the primary ore of aluminum. This ore undergoes refining through the Bayer process to produce alumina (aluminum oxide).
Step 1: Bauxite Mining: Extracting raw bauxite from mines.
Step 2: Bayer Process: Converting bauxite into alumina.
Smelting and Casting
The next phase involves transforming alumina into aluminum through the Hall-Héroult process, which uses electrolytic reduction.
Smelting: Alumina is dissolved in molten cryolite and subjected to electric current to produce molten aluminum.
Casting: The molten aluminum is cast into slabs or billets for rolling.
Rolling the Aluminum
The aluminum slabs are rolled into coils in multiple stages:
الدرفلة على الساخن
Process: Heated slabs are passed through rollers to reduce thickness.
Outcome: Produces a strong and malleable base material for further processing.
Cold Rolling
Process: Aluminum is further rolled at room temperature to achieve precise dimensions and surface finish.
Outcome: Creates thinner, smoother coils with improved strength.
Heat Treatment and Annealing
After rolling, the coils are subjected to heat treatment to adjust mechanical properties such as hardness and ductility. Annealing relieves internal stresses and ensures uniform quality.
Types of Aluminum Coils
Aluminum coils are categorized based on their alloy composition, temper, and application.
النوع | الوصف | التطبيقات |
---|---|---|
1xxx Series Aluminum | High purity, excellent corrosion resistance | Electrical applications, chemical equipment |
3xxx Series Aluminum | Manganese alloyed, good corrosion resistance | Roofing, siding, beverage cans |
5xxx Series Aluminum | Magnesium alloyed, high strength and corrosion resistance | Marine applications, automotive panels |
6xxx Series Aluminum | Silicon and magnesium alloyed, high strength and machinability | Structural components, bridges |
Coated Aluminum Coils | Coated with protective or decorative layers | Building facades, packaging |
Advantages of Aluminum Coils in Manufacturing
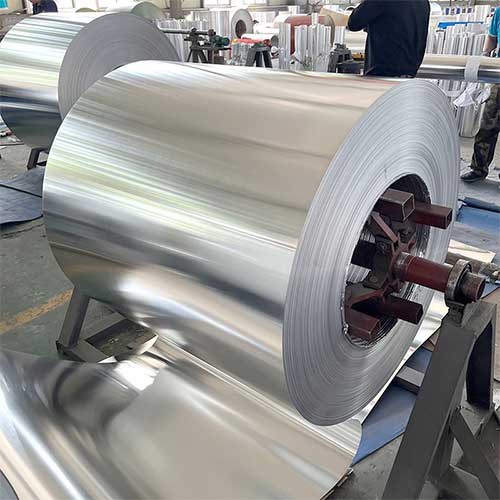
Lightweight and Durable
Aluminum’s low density makes it easy to transport and handle, while its durability ensures a long service life.
مقاومة التآكل
Aluminum naturally forms a protective oxide layer, making it ideal for outdoor and marine applications.
تعدد الاستخدامات
Aluminum coils can be customized in terms of size, thickness, and alloy composition to meet diverse industry requirements.
Sustainability
Aluminum is 100% recyclable without quality degradation, making it an eco-friendly material choice.
Common Applications of Aluminum Coils
الإنشاءات
Used for roofing, siding, and structural components due to their lightweight and corrosion-resistant properties.
السيارات
Aluminum coils contribute to lighter vehicle designs, improving fuel efficiency and reducing emissions.
Packaging
Food and beverage packaging extensively uses aluminum for its non-toxic and impermeable qualities.
Electrical and Electronics
Aluminum’s conductivity and corrosion resistance make it a preferred choice for electrical wiring and electronic casings.
Innovations in Aluminum Coil Production
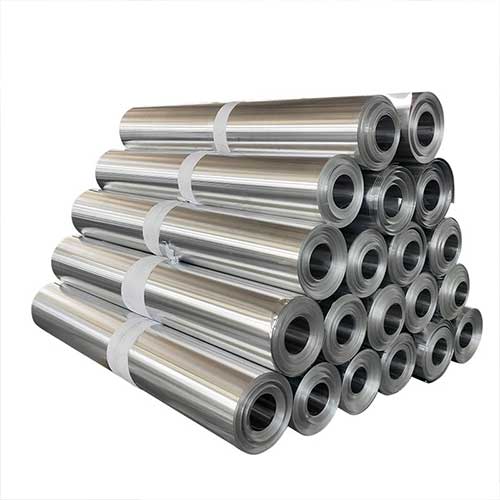
Advanced Rolling Techniques
Modern mills use automated systems for precision rolling and consistent quality.
Surface Treatments
Coatings and anodizing improve aesthetics and functional performance.
High-Efficiency Furnaces
Energy-efficient furnaces reduce emissions during heat treatment processes.
الخاتمة
Aluminum coils are the backbone of numerous industries, offering unmatched versatility and performance. From mining to rolling and finishing, the manufacturing process is a testament to engineering excellence. Understanding the intricacies of aluminum coil production not only highlights their importance but also helps manufacturers and consumers make informed decisions. Whether you’re in construction, automotive, or packaging, aluminum coils provide a sustainable, reliable, and high-performance solution for modern applications.
الأسئلة الشائعة
What are aluminum coils used for?
Aluminum coils are used in construction, automotive, packaging, and electrical applications due to their lightweight and corrosion-resistant properties.
What is the difference between hot-rolled and cold-rolled aluminum coils?
Hot-rolled aluminum coils are produced at high temperatures, resulting in a stronger and more malleable material. Cold-rolled aluminum coils are rolled at room temperature for a smoother finish and precise dimensions.
What alloys are commonly used in aluminum coils?
Common alloys include the 1xxx, 3xxx, 5xxx, and 6xxx series, each offering unique properties for specific applications.
What industries benefit the most from aluminum coils?
Industries such as construction, automotive, packaging, and electronics extensively use aluminum coils.
Why is aluminum considered a sustainable material?
Aluminum’s recyclability, energy-efficient production, and durability contribute to its status as a sustainable and eco-friendly material.