مرحبًا بك في مدونتي!
قبل أن نتعمق في المحتوى، أود أن تنضموا إليّ على منصات التواصل الاجتماعي الخاصة بي حيث أشارك المزيد من الأفكار وأتفاعل مع المجتمع وأنشر التحديثات. إليك كيف يمكنك التواصل معي:
فيسبوك : فيسبوكhttps://www.facebook.com/profile.php?id=61565500692293
والآن، لنبدأ رحلتنا معًا. آمل أن تجدوا المحتوى هنا ثاقباً وجذاباً وقيّماً.
جدول المحتويات
مقدمة
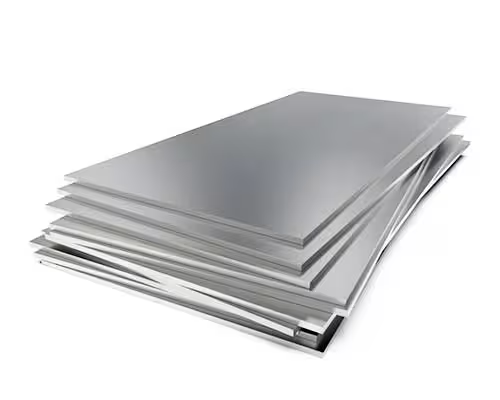
Aluminum plates serve as fundamental materials across numerous industries including aerospace, automotive manufacturing, construction, and marine engineering due to their exceptional combination of lightweight properties, corrosion resistance, and structural durability. When selecting aluminum plates for industrial or commercial applications, one of the most critical decisions involves choosing between thick aluminum plates and thin plates. Each type offers distinct advantages and limitations that make them suitable for specific use cases.
This comprehensive guide delves into the essential differences between thick aluminum plate and thin aluminum plates, examining their mechanical properties, manufacturing considerations, cost implications, and optimal applications. By understanding these key factors, engineers, procurement specialists, and fabricators can make informed decisions that align with their project requirements, performance expectations, and budgetary constraints.
Defining Thick Aluminum Plates
A thick aluminum plate is generally classified as any aluminum sheet material measuring 6 millimeters (0.25 inches) or greater in thickness. These plates are engineered to deliver superior structural integrity, making them indispensable in applications where high load-bearing capacity and resistance to mechanical stress are paramount.
Core Characteristics of Thick Aluminum Plates
Thick aluminum plates exhibit several defining properties that set them apart from their thinner counterparts:
- Exceptional Strength-to-Weight Ratio: Despite being heavier than thin plates, thick aluminum plates provide an outstanding balance between weight and strength, particularly when alloyed with elements like magnesium or zinc.
- Enhanced Rigidity and Stability: The increased thickness minimizes flexing and deformation under substantial loads, ensuring dimensional stability in structural frameworks.
- Superior Impact Resistance: Thick plates can withstand significant mechanical shocks and vibrations, making them ideal for military and aerospace applications.
- Improved Machinability for Heavy Fabrication: While requiring more robust machining equipment, thick plates can be precision-cut, drilled, and welded to meet exacting specifications.
Common Alloy Grades and Their Industrial Applications
الصف | Primary Alloying Elements | الخصائص الرئيسية | التطبيقات النموذجية |
---|---|---|---|
6061 | Magnesium, Silicon | High strength, excellent corrosion resistance | Aircraft components, structural beams, marine fittings |
5083 | Magnesium, Manganese | Superior weldability, seawater resistance | Ship hulls, offshore platforms, cryogenic tanks |
7075 | Zinc, Copper | Extreme tensile strength | Aerospace frames, military vehicle armor |
Understanding Thin Aluminum Plates
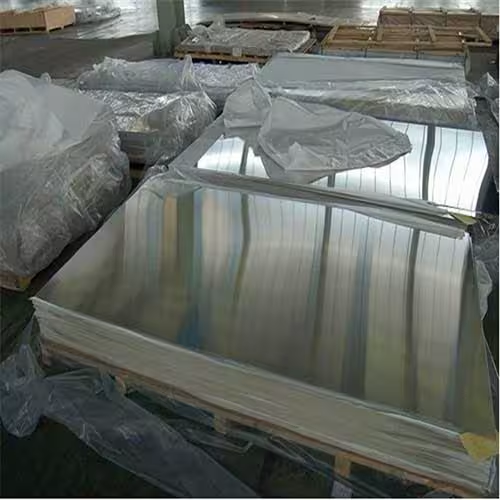
Thin aluminum plates are characterized by thicknesses below 6 millimeters (0.25 inches), offering distinct advantages in applications where weight reduction and formability take precedence over sheer structural strength.
Key Attributes of Thin Aluminum Plates
- Lightweight and Flexible: The reduced material thickness allows for easy handling and installation, particularly in large-scale manufacturing processes.
- Excellent Formability: Thin plates can be readily bent, stamped, or rolled into complex shapes without cracking, making them perfect for automotive body panels and decorative elements.
- Cost-Effective Production: Lower material requirements translate to reduced costs, especially in high-volume production runs.
- Optimal Thermal and Electrical Conductivity: Certain thin aluminum alloys are preferred in electronics and heat exchanger systems due to their efficient energy transfer properties.
Popular Alloy Grades for Thin Aluminum Plates
الصف | Primary Alloying Elements | الخصائص الرئيسية | التطبيقات النموذجية |
---|---|---|---|
3003 | المنجنيز | Good formability, moderate strength | HVAC systems, food packaging, roofing |
5052 | Magnesium | High fatigue resistance | Vehicle body panels, fuel tanks, electronic enclosures |
1100 | Pure Aluminum (99%) | Superior conductivity | Chemical equipment, electrical busbars, lighting fixtures |
Comparative Analysis: Thick vs Thin Aluminum Plates
Structural Performance Under Load
Thick aluminum plates demonstrate markedly better performance in load-bearing scenarios. Their substantial cross-sectional area provides inherent resistance to bending moments and compressive forces. In contrast, thin plates may exhibit noticeable deflection under similar loads, necessitating additional support structures in some applications.
Weight Considerations in Design
The weight disparity between thick and thin plates significantly impacts transportation logistics and installation processes. While thick plates contribute to overall structural mass, thin plates enable lightweight designs crucial in aerospace and automotive sectors where fuel efficiency is critical.
Fabrication Techniques and Limitations
Machining thick aluminum plates demands specialized equipment such as high-power plasma cutters and heavy-duty CNC milling machines. Welding procedures often require preheating to prevent thermal distortion. Conversely, thin plates can be processed using standard workshop tools, allowing for faster prototyping and lower fabrication costs.
Economic Factors in Material Selection
Material costs scale proportionally with thickness, making thick aluminum plates a considerable investment for large projects. Thin plates offer substantial savings in raw material expenses, though potential trade-offs in durability must be carefully evaluated based on application requirements.
Industry-Specific Applications
The choice between thick and thin plates frequently depends on sector-specific demands:
- Aerospace & Defense: Thick plates for airframe components and armor plating; thin plates for interior panels and ducting.
- Marine Engineering: Thick plates for hull construction; thin plates for cabin fixtures and decorative trim.
- الإنشاءات: Thick plates for load-bearing columns and bridges; thin plates for cladding and roofing systems.
Guidelines for Selecting the Appropriate Aluminum Plate
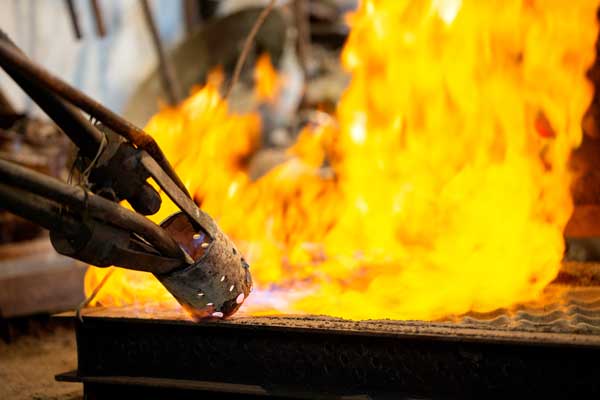
Several critical factors should guide the selection process:
- Mechanical Load Requirements: Assess whether the application involves static loads, dynamic stresses, or impact forces.
- الظروف البيئية: Consider exposure to corrosive elements, temperature extremes, or UV radiation.
- Manufacturing Constraints: Evaluate available fabrication capabilities and associated processing costs.
- Lifecycle Costs: Factor in maintenance requirements and potential replacement intervals.
الخاتمة
The decision between utilizing thick aluminum plates or thin variants represents a fundamental engineering consideration with far-reaching implications for product performance, manufacturing efficiency, and project economics. Thick plates deliver unmatched structural robustness for demanding applications, while thin plates provide versatile solutions for weight-sensitive and cost-conscious projects.
By systematically evaluating the comparative advantages outlined in this analysis, technical professionals can optimize their material selection to achieve ideal balance between strength, weight, and cost-effectiveness across diverse industrial applications.
الأسئلة الشائعة
What defines the threshold between thick and thin aluminum plates?
The industry standard typically classifies 6mm (0.25 inches) as the dividing line, with thicker gauges considered plate and thinner gauges as sheet.
How does alloy composition affect plate performance?
Alloying elements like magnesium enhance strength, while manganese improves formability. The 7xxx series offers highest strength but reduced corrosion resistance compared to 5xxx alloys.
Can thin aluminum plates be reinforced for structural applications?
Yes, through strategic ribbing, honeycomb cores, or composite lamination, though this adds complexity versus using thick plate material.
What surface treatments improve aluminum plate performance?
Anodizing increases corrosion resistance, while powder coating enhances durability. Chemical conversion coatings prepare surfaces for painting or adhesive bonding.
How does thermal expansion affect thick versus thin plates?
All aluminum expands similarly with heat, but thick plates exhibit greater dimensional stability due to their mass, while thin plates may show more noticeable movement.