Welcome to My Blog!
Before we dive into the content, I’d love for you to join me on my social media platforms where I share more insights, engage with the community, and post updates. Here’s how you can connect with me:
Facebook:https://www.facebook.com/profile.php?id=61565500692293
Now, let’s get started on our journey together. I hope you find the content here insightful, engaging, and valuable.
Table of Contents
Introduction
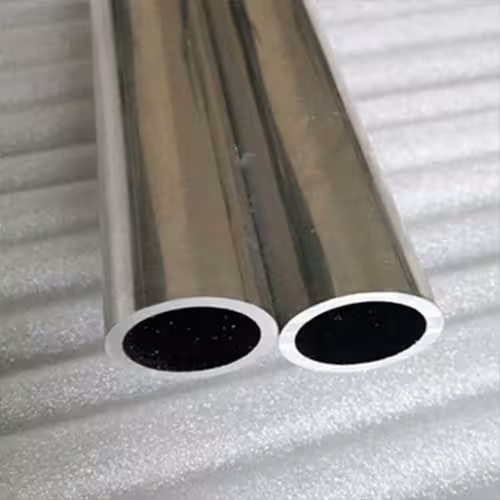
Alloy pipes are integral components in a wide range of industries due to their strength, durability, and resistance to corrosion. These pipes, made from combining metals like nickel, chromium, molybdenum, and more, provide enhanced performance characteristics over traditional carbon steel or stainless steel pipes. Understanding the various types of alloy pipes, their applications, and their benefits can help industries choose the right material for their specific needs.
This comprehensive guide explores the different types of alloy pipes, their applications in various industries, and the unique advantages they offer. We will also provide a detailed comparison table and address common questions in the FAQ section to aid in your decision-making process.
Understanding Alloy Pipes and Their Importance
What are Alloy Pipes?
Alloy pipes are manufactured by blending two or more metallic elements to achieve improved mechanical and chemical properties. Commonly used metals include chromium, nickel, molybdenum, and manganese. These combinations enhance properties like strength, corrosion resistance, and thermal stability, making alloy pipes suitable for demanding applications.
Importance of Alloy Pipes in Various Industries
Alloy pipes are essential in industries that require materials to withstand harsh conditions, such as high temperatures, pressures, or corrosive environments. Key sectors include:
- Oil and Gas
- Chemical Processing
- Power Generation
- Automotive and Aerospace
- Construction and Infrastructure
Types of Alloy Pipes
Low Alloy Steel Pipes
Low alloy steel pipes contain small amounts of alloying elements (typically less than 5% of total composition). These pipes offer improved mechanical properties over carbon steel while maintaining cost-effectiveness.
Applications: Structural components, pipelines, automotive parts.
High Alloy Steel Pipes
High alloy steel pipes have a higher concentration of alloying elements (more than 5%), providing exceptional corrosion resistance and strength.
Applications: Chemical processing, power plants, offshore oil drilling.
Nickel Alloy Pipes
Nickel alloy pipes offer excellent resistance to corrosion and heat. They are ideal for environments involving high temperatures or acidic substances.
Applications: Chemical processing, marine applications, power generation.
Chrome-Moly Alloy Pipes
These pipes combine chromium and molybdenum, offering enhanced high-temperature strength and corrosion resistance.
Applications: Boiler tubes, pressure vessels, oil and gas industry.
Stainless Alloy Pipes
Stainless alloy pipes contain chromium and nickel, providing excellent corrosion resistance and aesthetic appeal.
Applications: Food processing, medical equipment, decorative purposes.
Key Features and Properties of Alloy Pipes
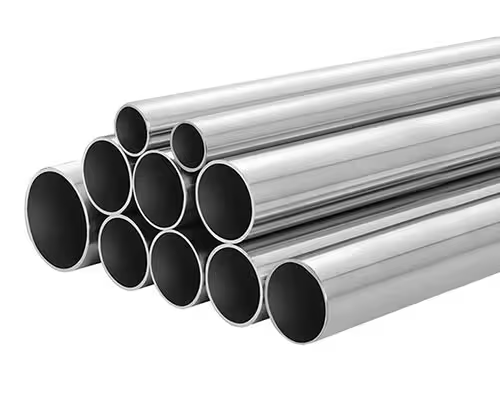
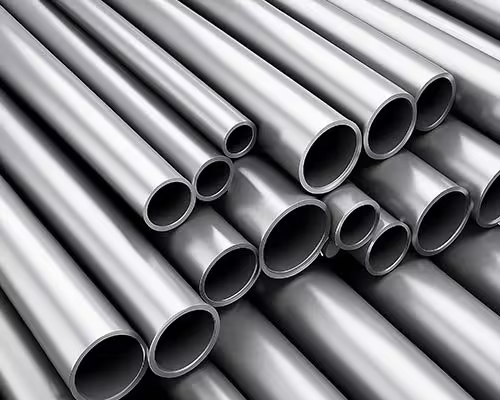
When selecting alloy pipes for your application, consider the following features and properties:
Strength and Durability
Alloy pipes are designed to withstand high pressures and heavy loads, making them suitable for critical applications.
Corrosion Resistance
Depending on the alloy composition, these pipes can resist corrosion in various environments, including acidic, alkaline, and marine conditions.
Thermal Stability
Alloy pipes maintain structural integrity at high temperatures, making them ideal for power plants and chemical processing facilities.
Weldability and Fabrication
Most alloy pipes can be easily welded and fabricated into complex shapes, supporting diverse industrial requirements.
Alloy Pipes Comparison Table
Below is a comparison table showcasing different types of alloy pipes and their primary characteristics:
Type of Alloy Pipe | Main Composition | Key Properties | Common Applications |
---|---|---|---|
Low Alloy Steel | Carbon, Manganese | Moderate strength, cost-effective | Automotive, construction |
High Alloy Steel | Chromium, Nickel | High strength, corrosion-resistant | Chemical processing, power plants |
Nickel Alloy | Nickel, Chromium | Excellent corrosion and heat resistance | Marine, aerospace |
Chrome-Moly Alloy | Chromium, Molybdenum | High-temperature strength | Boilers, oil and gas |
Stainless Alloy | Chromium, Nickel | Superior corrosion resistance, aesthetic | Food processing, medical |
Applications of Alloy Pipes in Various Industries
Oil and Gas Industry
Alloy pipes are essential in the oil and gas industry for transporting hydrocarbons under extreme pressures and temperatures. Chrome-Moly and nickel alloys are commonly used in pipelines and refinery equipment.
Chemical Processing
The chemical industry relies on high alloy and nickel alloy pipes for handling corrosive chemicals and aggressive fluids, ensuring safety and durability.
Power Generation
Power plants utilize alloy pipes in boilers, heat exchangers, and turbines, where high temperatures and pressures are common.
Automotive and Aerospace
Low alloy steel pipes are used in automotive structures for their lightweight yet strong characteristics, while nickel alloys are vital in aerospace for their heat resistance.
Construction and Infrastructure
In construction, alloy pipes offer enhanced load-bearing capacity and durability, making them suitable for bridges, buildings, and other infrastructure projects.
Benefits of Using Alloy Pipes
Enhanced Strength and Load Capacity
Alloy pipes provide superior strength, enabling them to carry heavy loads and withstand high-pressure environments.
Improved Corrosion Resistance
Resistance to rust and chemical corrosion extends the lifespan of alloy pipes, reducing maintenance costs.
Versatility in Applications
Alloy pipes are suitable for a wide range of applications due to their adaptability in various environments.
Cost Efficiency
Though initially more expensive than standard pipes, the durability and reduced maintenance costs of alloy pipes make them a cost-effective choice in the long run.
Maintenance and Inspection of Alloy Pipes
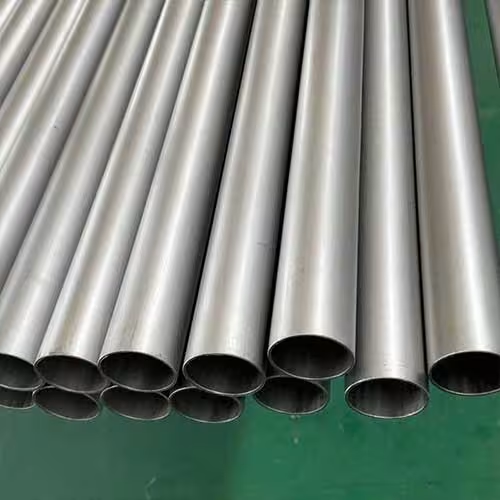
Regular maintenance and inspection are crucial for alloy pipes to ensure their longevity and performance. Key practices include:
- Regular Visual Inspection: Check for signs of corrosion, leaks, or damage.
- Non-Destructive Testing (NDT): Ultrasonic testing, magnetic particle testing, and radiographic testing help identify internal defects.
- Proper Cleaning: Use suitable cleaning agents to remove deposits and prevent corrosion.
- Monitoring Pressure and Temperature: Ensure operating conditions remain within the pipe’s specifications.
Conclusion
Alloy pipes are indispensable in modern industries due to their enhanced strength, corrosion resistance, and adaptability. By understanding the various types of alloy pipes, their applications, and benefits, industries can make informed decisions to optimize performance and cost-efficiency. Whether in oil and gas, chemical processing, power generation, or construction, alloy pipes provide reliable solutions for critical applications.
FAQ
What are alloy pipes made of?
Alloy pipes are made by combining metals such as chromium, nickel, molybdenum, and others to enhance strength, corrosion resistance, and thermal stability.
How do alloy pipes differ from carbon steel pipes?
Alloy pipes contain additional metallic elements that improve their mechanical and chemical properties, making them more durable and resistant to harsh conditions than carbon steel pipes.
Are alloy pipes suitable for high-temperature applications?
Yes, alloy pipes, especially chrome-moly and nickel alloys, are designed to withstand high temperatures, making them ideal for boilers, power plants, and chemical processing.
What industries use alloy pipes the most?
Key industries include oil and gas, chemical processing, power generation, automotive, aerospace, and construction.
How often should alloy pipes be inspected?
Regular inspections should be conducted annually or as per industry standards, with non-destructive testing methods used for critical applications.
Can alloy pipes be welded easily?
Yes, most alloy pipes are weldable, though specific welding techniques may be required depending on the alloy composition.
What factors affect the choice of alloy pipes?
Factors include operating temperature, pressure, corrosive environment, required strength, and cost considerations.