Welcome to My Blog!
Before we dive into the content, I’d love for you to join me on my social media platforms where I share more insights, engage with the community, and post updates. Here’s how you can connect with me:
Facebook:https://www.facebook.com/profile.php?id=61565500692293
Now, let’s get started on our journey together. I hope you find the content here insightful, engaging, and valuable.
Table of Contents
Introduction
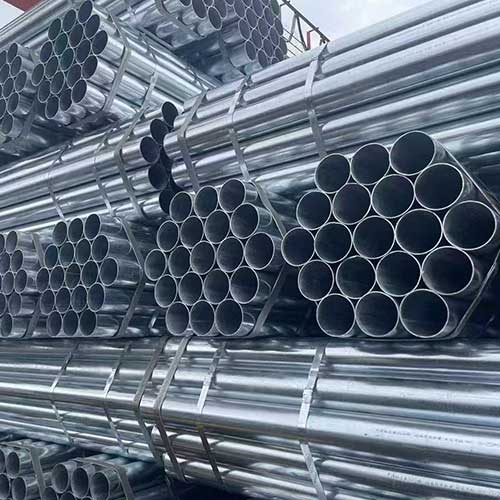
A seamless pipe production line refers to the automated machinery used to manufacture seamless pipes, which are pipes without welded seams. These pipes are highly valued in applications that require high strength, durability, and resistance to extreme conditions. The process typically involves stages such as piercing, elongation, heat treatment, and finishing, all of which must be executed with high precision.
A high-efficiency seamless pipe production line ensures maximum output while maintaining the desired quality and consistency of the final product. Efficiency in production translates to reduced energy consumption, lower costs, and a faster turnaround time, making it a valuable investment for manufacturers.
Key Feature 1: Advanced Technology Integration
One of the defining characteristics of a high-efficiency seamless pipe production line is the use of advanced technology. The integration of automated control systems, sensors, and monitoring devices allows the production line to operate at optimum performance. These technologies help in tracking every stage of production, ensuring that the process is running smoothly and any potential issues are identified early.
By employing sophisticated technologies, the production line can achieve higher throughput, precision in pipe dimensions, and improved surface finish. Additionally, real-time data collection from various parts of the line enables continuous optimization of processes, which helps in reducing waste and maximizing output.
Key Feature 2: High-Precision Machinery for Pipe Formation
The quality and consistency of the final product largely depend on the precision of the machinery used in the seamless pipe production line. High-efficiency lines use state-of-the-art equipment for each step of the manufacturing process, starting from billet heating and piercing to elongation and reduction.
For instance, advanced rotary piercing machines ensure that the billets are consistently pierced with minimal deformation. The elongation process, which transforms the pierced billet into a hollow pipe, is carried out using stretch reducing mills that can maintain a high degree of accuracy in diameter control. This precision helps in producing seamless pipes with uniform wall thickness and smooth internal surfaces.
Key Feature 3: Energy Efficiency and Sustainability
Energy efficiency is a significant factor in evaluating the performance of a seamless pipe production line. A high-efficiency line incorporates energy-saving technologies that reduce power consumption throughout the production process. This includes the use of regenerative burners for heating billets and optimizing the power usage of various machines on the line.
Moreover, sustainability has become a critical concern in modern manufacturing processes. High-efficiency seamless pipe production lines are designed to minimize energy consumption, reduce material waste, and lower CO2 emissions. By incorporating energy-efficient practices, manufacturers not only reduce operating costs but also contribute to environmental conservation.
Key Feature 4: Automation for Consistency and Speed
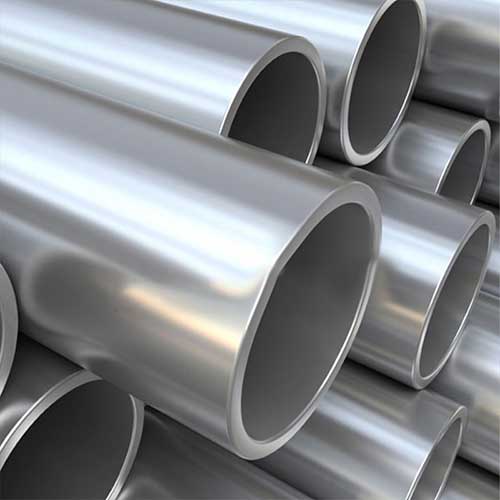
Automation plays a crucial role in enhancing the efficiency of a seamless pipe production line. Automated processes help maintain consistent quality while increasing production speed. With automated systems in place, the production line can operate continuously, with minimal human intervention. This helps in reducing labor costs and the likelihood of human error, leading to more consistent pipe quality.
In addition to reducing human involvement, automation systems are capable of adjusting parameters in real-time based on feedback from the production line. This dynamic adjustment process ensures that the pipes meet the required specifications without the need for manual intervention, thus boosting productivity.
Key Feature 5: Quality Control Systems
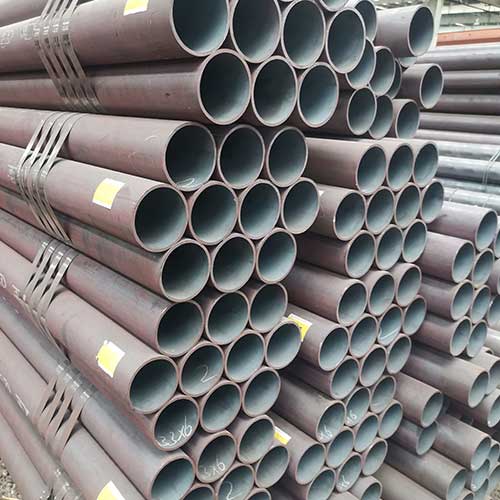
A high-efficiency seamless pipe production line integrates robust quality control systems at each stage of production. From billet inspection to final testing, these systems ensure that the pipes produced are of the highest quality. These systems include ultrasonic testing for detecting internal defects, visual inspection for surface quality, and dimensional measurement tools to ensure that the pipes meet the specified standards.
Having real-time quality control mechanisms in place allows manufacturers to identify and correct issues early in the production process. This results in fewer defective products, less waste, and a more reliable production line overall.
Table: Key Features of a High-Efficiency Seamless Pipe Production Line
Feature | Description | Benefits |
---|---|---|
Advanced Technology | Use of automated control systems and sensors for monitoring | Increased precision and real-time optimization |
High-Precision Machinery | Use of rotary piercing and stretch reducing mills | Consistent pipe dimensions and quality |
Energy Efficiency | Regenerative burners and energy-saving equipment | Reduced energy consumption and lower production costs |
Automation | Automated systems for minimal human intervention | Enhanced speed, consistency, and reduced labor costs |
Quality Control Systems | Real-time quality testing and inspection | Improved product quality and reduced defects |
Conclusion
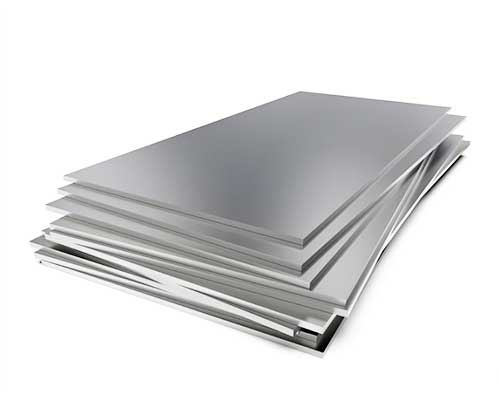
The seamless pipe production line is the backbone of industries that rely on high-quality pipes for structural integrity and performance. A high-efficiency production line ensures optimal output while maintaining the quality and precision required for demanding applications. The key features discussed in this blog—advanced technology integration, high-precision machinery, energy efficiency, automation, and quality control systems—are essential for achieving the best possible results.
Investing in a high-efficiency seamless pipe production line not only enhances productivity but also contributes to cost savings, sustainability, and better product consistency. Manufacturers that prioritize these features will be well-positioned to meet the growing demand for seamless pipes across various industries.
FAQ
What is the role of automation in a seamless pipe production line?
Automation helps to increase the production speed while ensuring consistent quality. It reduces the need for human intervention and allows for dynamic adjustments during the manufacturing process.
How does energy efficiency impact the cost of operating a seamless pipe production line?
Energy efficiency directly reduces the amount of power consumed during the production process, which lowers operating costs and makes the production line more sustainable.
What is the importance of precision machinery in seamless pipe production?
Precision machinery ensures that the pipes are formed to exact specifications, maintaining uniform wall thickness, diameter, and surface finish, which are crucial for the performance of the final product.
How do quality control systems enhance the seamless pipe production process?
Quality control systems, such as ultrasonic testing and dimensional measurements, allow manufacturers to identify and rectify any defects early in the process, ensuring that only high-quality pipes are produced.
Why should manufacturers invest in high-efficiency seamless pipe production lines?
Investing in high-efficiency production lines leads to higher throughput, better product quality, reduced waste, and lower operating costs, making it a smart decision for manufacturers looking to stay competitive in the market.