Introduction
Steel alloy pipes play a vital role in the manufacturing industry, offering a range of benefits such as enhanced strength, durability, and corrosion resistance. These pipes are a key component in many industrial applications, making them a popular choice for manufacturers. In this blog, we will explore the various advantages of using steel alloy pipes in manufacturing and how they contribute to improving production processes, efficiency, and product quality.
By the end of this article, you will have a comprehensive understanding of why steel alloy pipes are essential for modern manufacturing industries and how to select the right type for your specific needs.
Understanding Steel Alloy Pipe
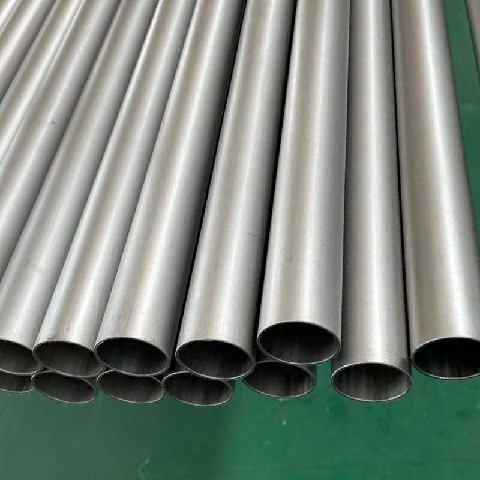
What Is a Steel Alloy Pipe?
A steel alloy pipe is made from steel mixed with one or more alloying elements, such as chromium, nickel, or molybdenum. These additional elements enhance the properties of the steel, making the pipes more resistant to wear, heat, and corrosion, while also increasing their strength and durability.
Steel alloy pipes are commonly used in industries such as construction, automotive, aerospace, oil and gas, and chemical processing, where reliability and longevity are essential.
Key Properties of Steel Alloy Pipe
Strength: Alloying elements like chromium and molybdenum significantly improve the tensile strength of the steel.
Corrosion Resistance: Elements such as nickel and chromium help protect the pipe from rust and corrosion.
Heat Resistance: Steel alloy pipes can withstand higher temperatures, making them ideal for applications that involve heat and pressure.
Versatility: These pipes can be tailored to meet specific industry needs by adjusting the alloy composition.
Advantages of Steel Alloy Pipe in Manufacturing
Enhanced Durability and Longevity
One of the most significant benefits of using steel alloy pipes in manufacturing is their superior durability. These pipes are designed to withstand harsh environments, such as extreme temperatures, high pressure, and corrosive substances. This makes them ideal for industries that require long-lasting materials that can maintain structural integrity under stress.
Steel alloy pipes also reduce the need for frequent maintenance and replacements, leading to lower operational costs over time. For manufacturers, this translates into fewer disruptions in production and increased efficiency.
High Strength-to-Weight Ratio
Steel alloy pipes offer an excellent strength-to-weight ratio, making them both strong and relatively lightweight. This is especially important in industries where the weight of the materials used can affect overall efficiency and performance. For example, in the automotive and aerospace industries, using lightweight yet strong materials is crucial for improving fuel efficiency and performance.
The high strength of steel alloy pipes means they can carry heavy loads without bending or breaking, making them a reliable option for construction and structural applications.
Improved Corrosion Resistance
One of the primary reasons manufacturers prefer steel alloy pipes is their exceptional resistance to corrosion. When exposed to moisture, chemicals, or extreme temperatures, steel alloy pipes are far less likely to corrode compared to traditional carbon steel pipes. This property is particularly valuable in industries such as oil and gas, where pipes are exposed to harsh environmental conditions.
The corrosion resistance of steel alloy pipes helps extend the lifespan of equipment, reducing maintenance costs and preventing potential safety hazards caused by rusted or weakened pipes.
Heat Resistance for High-Temperature Applications
Steel alloy pipes are commonly used in manufacturing processes that involve high heat or pressure. The addition of elements like chromium and molybdenum allows these pipes to maintain their structural integrity at high temperatures, making them ideal for applications such as boiler tubes, heat exchangers, and power plants.
Industries like chemical processing and power generation benefit significantly from using steel alloy pipes due to their ability to withstand intense heat without losing strength or performance.
Cost-Effectiveness
While the initial cost of steel alloy pipes may be higher than that of carbon steel pipes, their long-term cost-effectiveness makes them a wise investment for manufacturers. The durability, corrosion resistance, and low maintenance requirements of steel alloy pipes mean that they offer excellent value over time, reducing the need for frequent replacements and repairs.
Table: Comparison of Carbon Steel vs. Steel Alloy Pipe
Property | Carbon Steel Pipe | Steel Alloy Pipe |
---|---|---|
Strength | Lower | Higher due to alloying elements |
Corrosion Resistance | Prone to corrosion in moist settings | Highly resistant to corrosion |
Heat Resistance | Limited | Excellent in high-temperature conditions |
Durability | Susceptible to wear and tear | Longer-lasting and more durable |
Cost | Lower initial cost | Higher initial cost but more cost-effective over time |
Applications of Alloy Pipe in Manufacturing
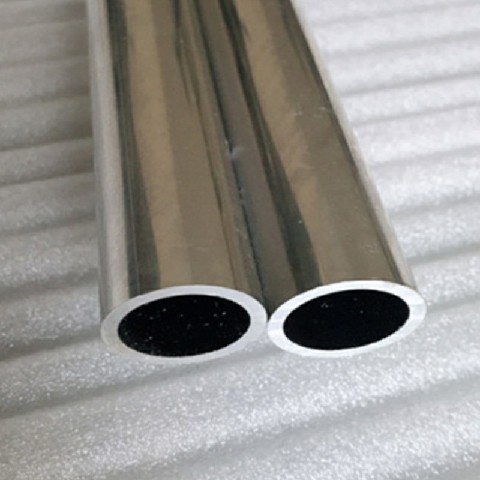
Oil and Gas Industry
The oil and gas industry heavily relies on alloy pipes for transportation of petroleum and natural gas. The ability of these pipes to resist corrosion and withstand high pressure makes them ideal for offshore drilling, pipeline infrastructure, and refineries.
Power Generation
Steel alloy pipes are used in the power generation industry for applications such as boiler tubes, where high heat resistance is essential. The pipes are capable of operating in extreme temperatures, ensuring the efficient transfer of heat within power plants.
Chemical Processing
In chemical plants, where corrosive substances and high temperatures are common, alloy pipes provide excellent durability and resistance. They are often used in the construction of chemical reactors, piping systems, and storage tanks.
Automotive Industry
Steel alloy pipes are used in automotive exhaust systems due to their ability to withstand high temperatures and resist corrosion. Their high strength-to-weight ratio also makes them suitable for lightweight yet strong components in vehicles.
Aerospace Industry
In the aerospace sector, alloy pipes are used for their strength, heat resistance, and lightweight properties. They are commonly found in aircraft engines, hydraulic systems, and structural components.
Conclusion
Steel alloy pipes offer numerous benefits to the manufacturing industry, from enhanced durability and corrosion resistance to superior heat tolerance and cost-effectiveness. Their versatility and ability to meet the stringent demands of various industries make them an indispensable component in modern manufacturing.
By understanding the advantages of alloy pipes and selecting the right supplier, manufacturers can improve operational efficiency, reduce costs, and ensure the longevity of their equipment.
FAQ
What is the main advantage of steel alloy pipes in manufacturing?
The main advantage is their superior durability and resistance to corrosion, heat, and pressure, which makes them ideal for various industrial applications.
How do steel alloy pipes differ from carbon steel pipes?
Steel alloy pipes are made by adding alloying elements like chromium and molybdenum to carbon steel, enhancing their strength, corrosion resistance, and heat tolerance.
Are alloy pipes more expensive than carbon steel pipes?
Yes, alloy pipes tend to be more expensive initially, but their long-term cost-effectiveness makes them a better investment for industries requiring durable and low-maintenance materials.
What industries benefit the most from using alloy pipes?
Industries such as oil and gas, power generation, chemical processing, automotive, and aerospace benefit greatly from the use of alloy pipes due to their strength, durability, and resistance to extreme conditions.
Can alloy pipes be customized for specific manufacturing needs?
Yes, alloy pipes can be tailored to meet specific industry requirements by adjusting the composition of alloying elements, ensuring optimal performance in different applications.