Welcome to My Blog!
Before we dive into the content, I’d love for you to join me on my social media platforms where I share more insights, engage with the community, and post updates. Here’s how you can connect with me:
Facebook:https://www.facebook.com/profile.php?id=61565500692293
Now, let’s get started on our journey together. I hope you find the content here insightful, engaging, and valuable.
Table of Contents
Introduction
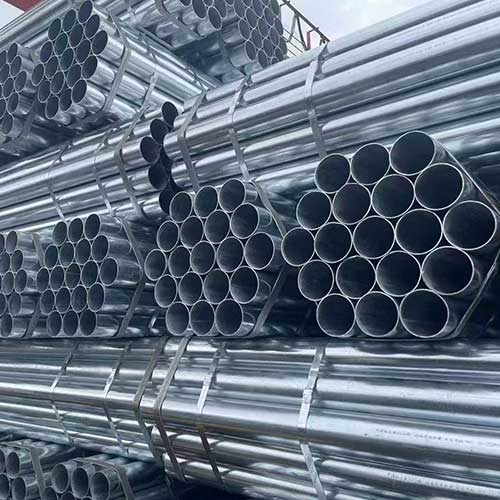
When it comes to industrial applications, choosing the right type of pipe is crucial. The debate between seamless vs welded pipe is often a significant consideration for engineers and project managers. Both types of pipes have distinct advantages and are suited for different purposes. This blog will explore the five key differences between seamless vs welded pipe to help you make an informed decision.
Understanding Seamless Pipes
Seamless pipes are created without any joints or welds, making them ideal for high-pressure environments. Their production involves a process where solid steel billets are heated and stretched into a tubular shape.
Characteristics of Seamless Pipes
- No Welding Required: Seamless pipes are formed entirely without welding, ensuring a uniform structure.
- High Durability: The absence of seams makes these pipes highly resistant to pressure and mechanical stress.
- Uniform Surface: Seamless pipes have a smooth interior and exterior surface, ideal for precision applications.
Seamless pipes are widely used in industries like oil and gas, chemical processing, and power generation due to their reliability in critical applications.
Overview of Welded Pipes

Welded pipes are manufactured by rolling flat steel plates or strips into a tubular shape and then welding the edges together. This process makes them more cost-effective compared to seamless pipes.
Characteristics of Welded Pipes
- Welded Joint Present: A visible seam runs along the length of the pipe.
- Cost-Effective: The production process requires less material and energy.
- Customizable Sizes: Welded pipes can be produced in various diameters and lengths.
Welded pipes are often used in applications where high pressure is not a primary concern, such as water distribution and construction.
Key Differences Between Seamless vs Welded Pipe
Manufacturing Process
- Seamless Pipes: Produced through extrusion, where solid billets are shaped into a pipe form without welding.
- Welded Pipes: Created by welding the edges of rolled steel sheets.
Strength and Durability
- Seamless Pipes: Offer superior strength due to their homogeneous structure and lack of a welded seam.
- Welded Pipes: While strong, the welded seam can be a weak point under extreme pressure.
Cost and Availability
- Seamless Pipes: Generally more expensive because of their complex manufacturing process.
- Welded Pipes: More affordable and widely available due to simpler production techniques.
Application Suitability
- Seamless Pipes: Ideal for high-pressure and high-temperature environments.
- Welded Pipes: Suited for applications with moderate pressure and structural uses.
Size Range
- Seamless Pipes: Limited in size, especially for larger diameters.
- Welded Pipes: Available in a broader range of sizes, including very large diameters.
Table Comparing Seamless vs Welded Pipe
Aspect | Seamless Pipe | Welded Pipe |
---|---|---|
Manufacturing Process | Extrusion without welding | Rolling and welding steel sheets |
Strength | High strength, no seam | Moderate strength, seam present |
Cost | Higher cost | Cost-effective |
Pressure Handling | Excellent for high-pressure uses | Suitable for moderate pressures |
Size Range | Limited, especially in large diameters | Broad, includes very large diameters |
Common Applications of Seamless vs Welded Pipe
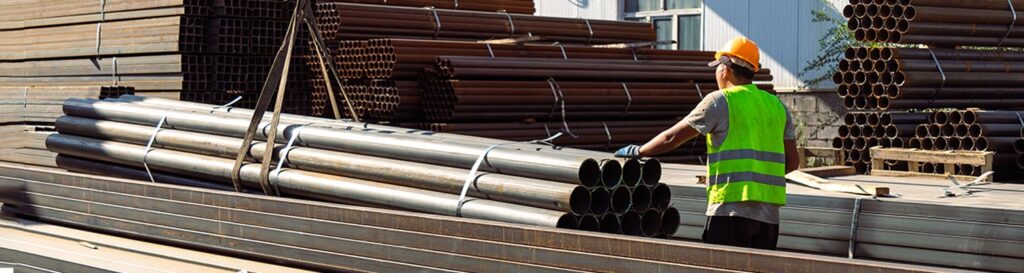
Industries Using Seamless Pipes
Seamless pipes are favored in industries where reliability and performance are critical, including:
- Oil and Gas Exploration
- Power Generation
- Aerospace
Industries Using Welded Pipes
Welded pipes are more common in applications where cost and customization are key, such as:
- Water Supply Systems
- Structural Frameworks
- Low-Pressure Chemical Transport
Factors to Consider When Choosing Between Seamless vs Welded Pipe
Project Requirements
When selecting between seamless vs welded pipe, it’s crucial to evaluate your project’s specific requirements. Start by identifying the intended use of the pipe and the conditions it will face. For high-pressure applications, seamless pipes are often the preferred choice due to their superior strength and ability to withstand extreme conditions. If your project involves moderate pressure or structural use, welded pipes may be a more cost-effective option.
The size of the pipe is another critical factor. Seamless pipes have limitations in terms of diameter, especially for larger sizes, while welded pipes offer greater flexibility and availability in a broader range of dimensions. Budget constraints should also guide your decision—seamless pipes typically come with higher upfront costs but may prove worthwhile for projects that demand long-term reliability and performance.
Material Compatibility
Choosing the right material for your pipe is essential to ensure optimal performance in your application. Seamless and welded pipes can be made from various materials such as carbon steel, stainless steel, or alloy steel, each suited for different environments.
For corrosive environments, like chemical processing plants, stainless steel pipes (both seamless and welded) may be ideal due to their resistance to rust and chemical damage. In high-temperature scenarios, such as power plants or refineries, seamless pipes made from heat-resistant alloys are often the better choice.
Consult material standards and industry specifications to ensure that the pipe material aligns with the mechanical and chemical requirements of your project. Incorrect material selection can lead to premature failure and costly replacements.
Long-Term Costs
While the upfront costs of seamless pipes are typically higher, their durability and resistance to mechanical stress can lead to significant savings over time. In critical applications where pipe failure could result in downtime, safety hazards, or expensive repairs, the initial investment in seamless pipes is often justified.
On the other hand, welded pipes, with their lower production costs, can be a practical choice for non-critical applications. For projects with tight budgets or temporary installations, welded pipes offer excellent value.
It’s essential to factor in the total lifecycle cost of the pipes, including maintenance, repair, and replacement expenses. Seamless pipes often require less frequent inspections and repairs due to their uniform structure, while welded pipes may need more attention at the seam, especially in high-stress environments.
Conclusion
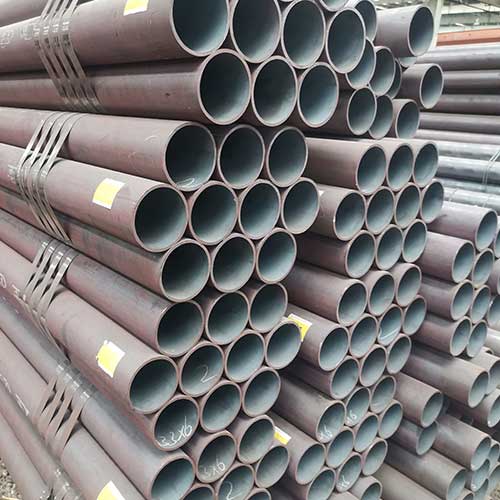
The choice between seamless vs welded pipe depends on the specific requirements of your project. Seamless pipes excel in high-pressure and high-temperature applications, while welded pipes are a cost-effective solution for low to moderate pressure environments. Understanding their differences ensures optimal performance and efficiency in your applications.
FAQ
What is the main difference between seamless vs welded pipe?
The main difference lies in their manufacturing process. Seamless pipes are made without welding, while welded pipes involve joining steel sheets or strips.
Are seamless pipes stronger than welded pipes?
Yes, seamless pipes generally have higher strength due to their homogeneous structure without a seam.
Which pipe is more cost-effective?
Welded pipes are more cost-effective due to their simpler manufacturing process and wider availability.
Can welded pipes be used for high-pressure applications?
While welded pipes can handle moderate pressure, seamless pipes are better suited for high-pressure environments.
How do I choose between seamless vs welded pipe?
Consider your project’s specific requirements, including pressure ratings, size, budget, and application environment, to make the best choice.